The Science Behind Porosity: A Comprehensive Guide for Welders and Fabricators
Recognizing the complex systems behind porosity in welding is critical for welders and fabricators pursuing remarkable craftsmanship. As metalworkers look into the midsts of this phenomenon, they uncover a globe controlled by numerous factors that influence the formation of these small voids within welds. From the composition of the base products to the complexities of the welding procedure itself, a plethora of variables conspire to either worsen or ease the visibility of porosity. In this thorough guide, we will unwind the scientific research behind porosity, discovering its effects on weld quality and introduction progressed techniques for its control. Join us on this journey through the microcosm of welding imperfections, where accuracy satisfies understanding in the quest of remarkable welds.
Comprehending Porosity in Welding
FIRST SENTENCE:
Assessment of porosity in welding reveals vital insights into the honesty and high quality of the weld joint. Porosity, defined by the presence of tooth cavities or gaps within the weld steel, is an usual issue in welding procedures. These spaces, otherwise properly dealt with, can jeopardize the structural honesty and mechanical residential properties of the weld, bring about possible failures in the ended up item.
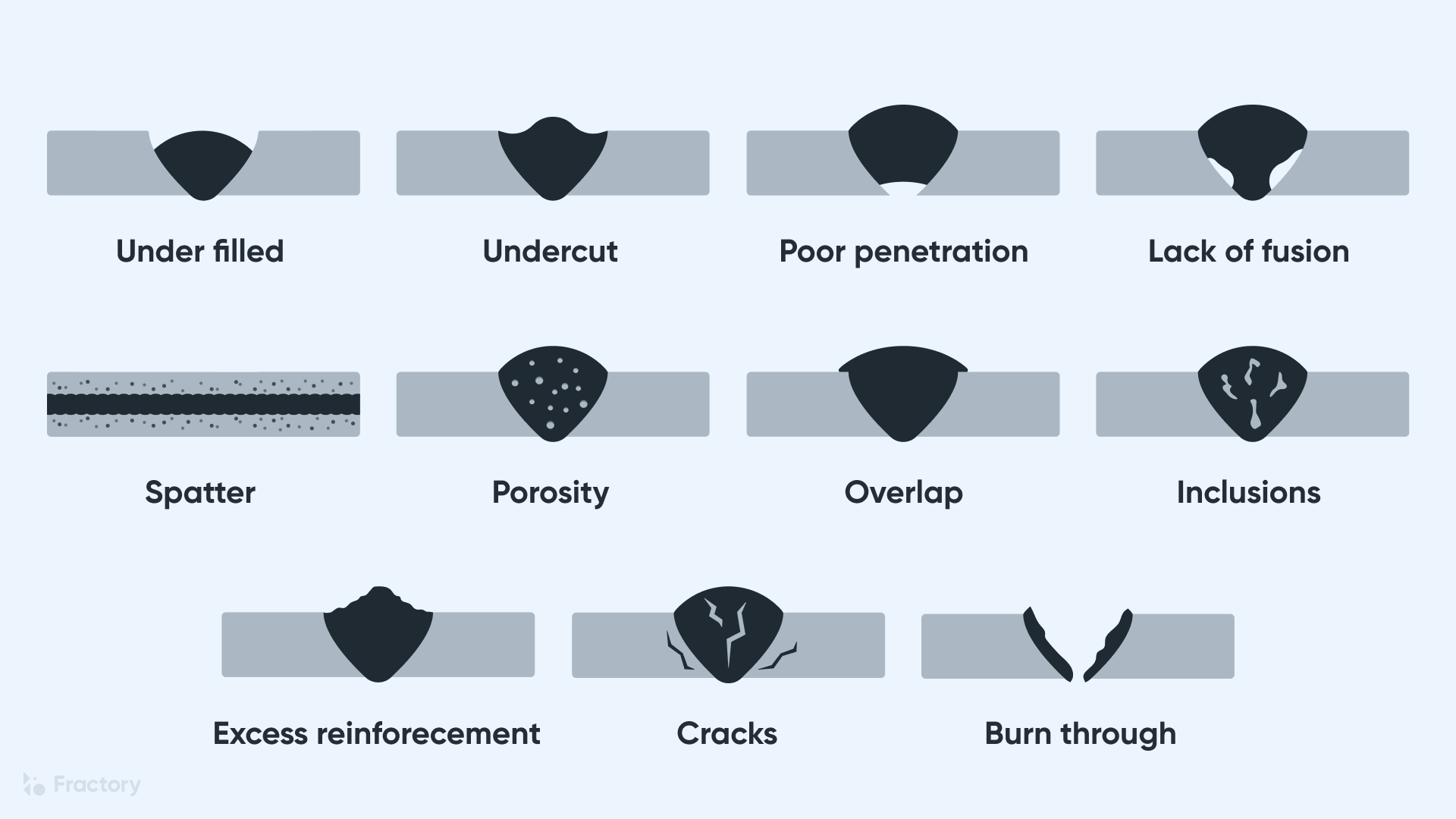
To detect and measure porosity, non-destructive testing techniques such as ultrasonic screening or X-ray examination are often employed. These methods permit for the recognition of inner defects without compromising the honesty of the weld. By evaluating the size, form, and circulation of porosity within a weld, welders can make educated choices to enhance their welding processes and accomplish sounder weld joints.

Factors Influencing Porosity Development
The incident of porosity in welding is influenced by a myriad of aspects, ranging from gas protecting effectiveness to the complexities of welding criterion settings. Welding specifications, including voltage, current, take a trip speed, and electrode kind, also influence porosity formation. The welding method used, such as gas metal arc welding (GMAW) or protected metal arc welding this website (SMAW), can influence porosity development due to variations in heat circulation and gas protection - What is Porosity.
Results of Porosity on Weld High Quality
The presence of porosity likewise damages the weld's resistance to corrosion, as the entraped air or gases within the voids can react with the surrounding environment, leading to destruction over time. Furthermore, porosity can impede the weld's capability to withstand pressure or impact, further jeopardizing the general high quality and dependability of the welded structure. In important applications such as aerospace, automotive, or architectural building and constructions, where security and resilience are critical, the harmful results of porosity on weld quality can have extreme consequences, stressing the importance of lessening porosity via correct welding methods and treatments.
Techniques to Minimize Porosity
To boost the quality of bonded joints and guarantee structural honesty, welders and fabricators employ specific methods aimed at reducing the formation of gaps and dental caries within the product during the welding procedure. One effective technique to decrease porosity is to guarantee proper product prep work. This includes thorough cleaning of the base steel to eliminate any type of contaminants such as oil, oil, or dampness that can contribute to porosity formation. Furthermore, utilizing the ideal welding parameters, such as the right voltage, existing, and take a trip rate, is essential in stopping porosity. Keeping a regular arc length and angle during welding also helps in reducing the probability of porosity.

Making use of the ideal welding strategy, such as back-stepping or using a weaving motion, can additionally help distribute heat equally and decrease the chances of porosity development. By implementing these techniques, welders can efficiently reduce porosity and generate top quality bonded joints.
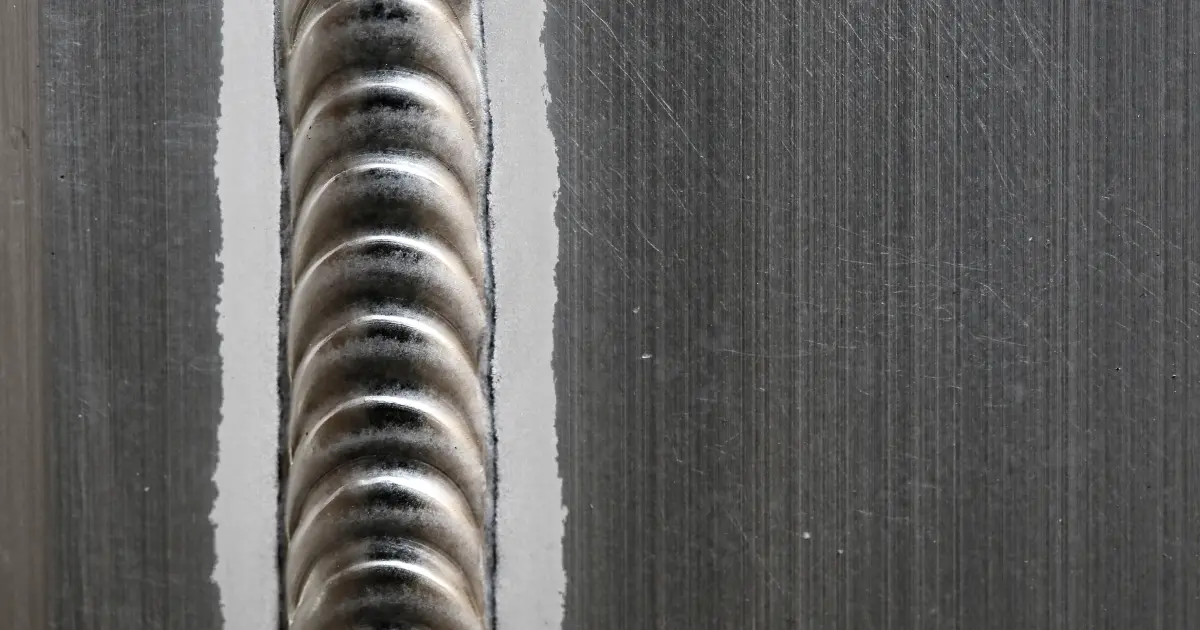
Advanced Solutions for Porosity Control
Applying sophisticated innovations and ingenious methods plays an essential role in achieving premium control over porosity in welding processes. One innovative option is making use of advanced gas blends. Shielding gases like helium or a mix of argon and hydrogen can help minimize porosity by providing better arc stability and improved gas insurance coverage. In addition, using advanced welding techniques such as pulsed MIG welding or changed atmosphere welding can additionally assist reduce porosity issues.
One more advanced home solution entails the usage of advanced welding equipment. As an example, making click to read use of equipment with integrated features like waveform control and sophisticated source of power can improve weld top quality and reduce porosity risks. Additionally, the execution of automated welding systems with specific control over specifications can dramatically decrease porosity problems.
Furthermore, incorporating sophisticated tracking and evaluation innovations such as real-time X-ray imaging or automated ultrasonic screening can assist in discovering porosity early in the welding process, permitting instant rehabilitative actions. In general, incorporating these sophisticated remedies can greatly improve porosity control and enhance the total quality of bonded parts.
Verdict
Finally, understanding the science behind porosity in welding is essential for welders and producers to produce top notch welds. By identifying the aspects affecting porosity development and executing methods to decrease it, welders can boost the total weld quality. Advanced services for porosity control can better boost the welding process and ensure a solid and reputable weld. It is necessary for welders to continually enlighten themselves on porosity and carry out finest techniques to attain ideal outcomes.